Many of the plastic and rubber products around us contain a chemical substance generally called filler. In this article, we will broadly introduce the roles, types, shapes, handling methods, and more about fillers.
What is a Filler?
A filler is defined as a general term for additives added to achieve high physical properties, high functionality, or to reduce production costs; it is a key material in various composite materials (according to the Filler Society of Japan).
Composite materials refer to materials produced from two or more constituent materials with different physical properties to achieve a better end-product. Example of these are compounds like PET (polyethylene terephthalate), PE (polyethylene), PP (polypropylene), PVC (polyvinyl chloride), and natural rubber, being combined with various additives.
Plastic and rubber substrates cannot be used as products such as tableware, buckets, computer cases, and tires if they are molded as they are. This is because they usually have insufficient strength or are prone to deterioration from temperature or light. Therefore, by mixing in additives such as fillers, the necessary functions are imparted to the products.
The Filler Society of Japan was established by researchers and corporate developers focusing on the basics and applied research of fillers, following the start of full-scale plastic and rubber production in Japan. As of 2022, there are 221 corporate members and 59 individual members registered.
Roles of Filler
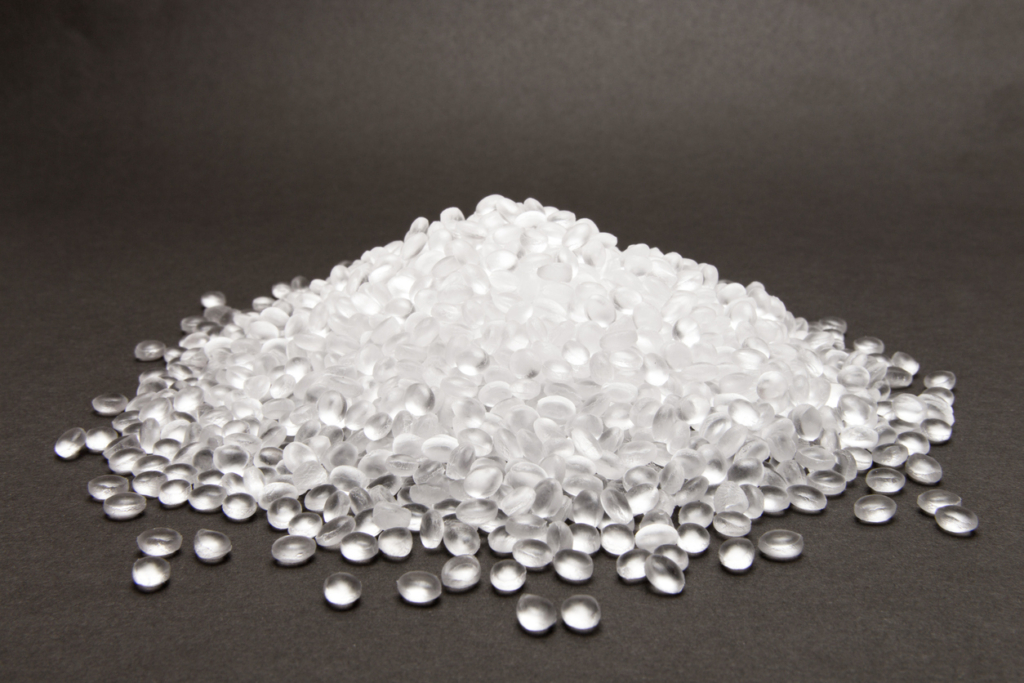
Composite materials require various functions, such as material strength, plasticity, antibacterial properties, weight reduction, piezoelectricity, lubricity, thermal insulation, electromagnetic wave absorption, light reflection and scattering control, dehumidification and dehydration, anti-blocking, and oil absorption. By incorporating fillers into plastic and rubber substrates, these various functions can be realized; it is thanks to the effects of fillers that we can conveniently use plastic and rubber products in our daily lives.
Types of Filler
The table below summarizes the chemical structures used and the functions imparted for each type of filler. Even from this, you can see that a diverse range of chemical substances are used.
Type of Filler | Chemical Structure Used | Functions Imparted |
Fiber-based | Carbon fiber, glass fiber, aramid fiber, fiber gypsum, etc. | Strength, conductivity, vibration damping |
Carbon-based | Carbon black, graphite, carbon fiber, charcoal powder, etc. | Conductivity, heat radiation |
Nitride-based | AlN (aluminum nitride), BN (boron nitride), etc. | Thermal conductivity |
Hydroxide-based | Aluminum hydroxide, magnesium hydroxide, etc. | Flame retardancy |
Ferrite-based | Iron oxide, samarium-cobalt magnet (Sm-Co), Nd-Fe-B magnet, etc. | Magnetism |
Mineral-based | Mica, clay, zeolite, activated clay, etc. | Gas barrier, deodorization, gas absorption |
Oxide-based | Titanium oxide, zinc oxide, iron oxide, calcium oxide, magnesium oxide, antimony oxide, etc. | UV protection, absorbents, flame retardants |
Metal powder-based | Iron powder, copper powder, etc. | Soundproofing, radiation protection |
Others | Barium sulfate, zinc borate, red phosphorus, zinc carbonate, hydrotalcite, dawsonite, molybdenum disulfide, Teflon powder, etc. | Various other functions |
Shapes of Filler
The shapes of fillers can be broadly classified into three categories: spherical, needle-like/fibrous, and plate-like. Each of these fillers have their own characteristics and is used according to the functions required for the product.
Spherical Fillers
Spherical fillers are suitable for products that require high impact resistance and control of thermal expansion. They mix evenly into plastic and rubber substrates, making them easy to process and allowing the composite material to uniformly exhibit its functions.
Needle-like/Fibrous Fillers
Needle-like/fibrous fillers are effective when enhancing the strength of plastic products. They also contribute to reinforcing composite materials and improving heat resistance. Carbon fiber and glass fiber are typical examples of needle-like/fibrous fillers. However, these types of fillers are said to pose challenges in molding stability and processability, requiring advanced techniques for composite material processing.
Plate-like Fillers
Plate-like fillers are effective for improving the strength of composite materials, vibration dampening, blocking gases, and imparting smoothness to surfaces. Maintaining molding stability with this type of filler is also challenging, and it is considered difficult to process due to its high level of difficulty.
Handling Methods of Filler
We will explain the handling methods of fillers: the preprocessing of fillers themselves and the blending of fillers with plastic or rubber substrates.
Preprocessing of Fillers
When blending fillers into plastic or rubber substrates, chemical preprocessing is often applied to the surface of the filler particles themselves. The purpose of this treatment is to prevent aggregation of filler particles and to enhance compatibility with the substrate, making them more easily blendable.
Blending Fillers with Materials
Blending fillers into plastic or rubber substrates, or kneading them together, is referred to as “compounding.” The main methods for compounding fillers into substrates are through using devices like extruders, rolls, or kneaders.
Rolls are commonly used for compounding with rubber substrates, where the rotation of the rolls presses and mixes the rubber with the filler. A kneader is a specialized machine used for mixing solids together. Fillers and plastic or rubber substrates are kneaded under pressure inside the kneader.
An extruder is also a specialized device for compounding solids. Material and additives like fillers are simultaneously fed into the hopper, then compounded inside the machine.
Handling Methods of Filler
Because there are various types of fillers, let’s introduce some leading filler manufacturers.
Classification of Filler | Type of Filler | Manufacturer Name |
Fiber-based | Carbon fiber | Toray Industries, Inc. |
Teijin Ltd. | ||
Mitsubishi Chemical Corporation | ||
Carbon-based | Carbon black | Asahi Carbon Co., Ltd. |
Tokai Carbon Co., Ltd. | ||
Nitride-based | AlN (Aluminum Nitride) | Tokuyama Corporation |
Furukawa Electric Co., Ltd. | ||
Hydroxide-based | Aluminum hydroxide | Tomoe Engineering Co., Ltd. |
Nippon Light Metal Co., Ltd. | ||
Ferrite-based | Samarium Cobalt magnet (Sm-Co) | Shin-Etsu Chemical Co., Ltd. |
Mineral-based | Mica | TOPY INDUSTRIES, LIMITED |
Oxide-based | Titanium oxide | Ishihara Sangyo Kaisha, Ltd. |
Sakai Chemical Industry Co., Ltd. |
Conclusion
Fillers are chemical substances mixed and kneaded into plastic and rubber products as additives to enhance its material properties. Composite materials based on plastic and rubber utilize the chemical and physical properties of fillers to create products that enrich our lives. There are many companies in Japan manufacturing and selling fillers, and detailed information can be obtained from each company’s website.
CrowdChem Inc. has launched the ‘CrowdChem Data Platform,’ which provides knowledge and insights in the field of chemistry, including catalog information of products categorized as fillers and patent information associated with these products. Some services are available for free, so please take advantage of them.
For a free trial of the ‘CrowdChem Data Platform,’ click below.
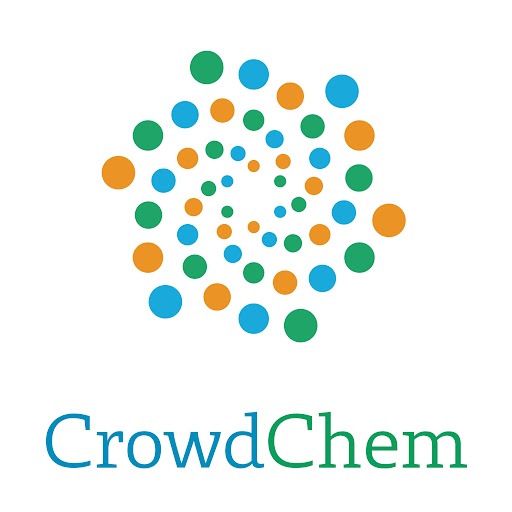